This research project, initiated by Juteborg Sweden AB, and co-financed by Lighter member programme, has shown great potential to produce the most sustainable and lightweight particleboard in the world, JutePart™️ with Ecohesives®️.
Here, Juteborg is replacing wood with Jute stick, and the fossil-based and toxic formaldehyde glue is replaced with a biobased, non-hazardous glue.
Juteborg Sweden AB in collaboration with the inventors of the bio-based glue Ecohesives®️ – researchers at KTH Royal Institute of Technology, Department of Fibre and Polymer Technology – have together succeeded and exceeded expectations.
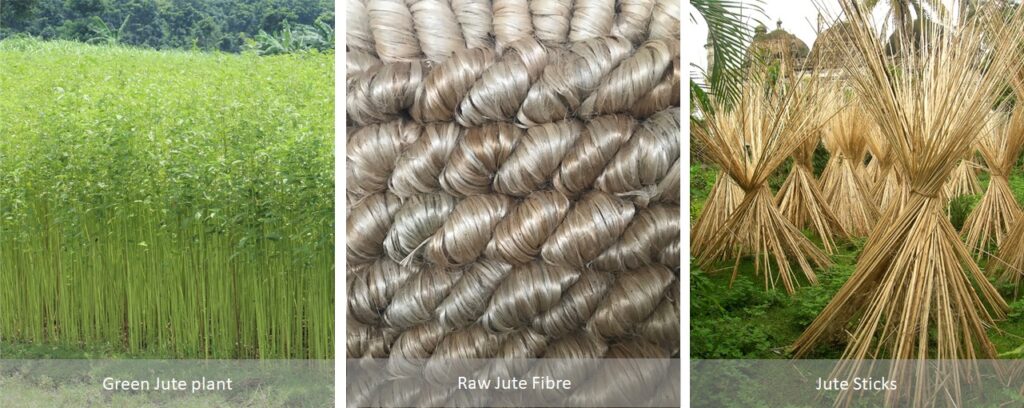
Particleboards were prepared from Jute-stick particles (residual material, almost treated like a waste, from jute-fibre production) and a bio-based, formaldehyde-free, adhesive (from side streams from the forest industry).
Juteborg Sweden AB predicted the board to be 25-30% more lightweight than the common wooden particleboards on the market. The results showed that the weight was almost 50% lower, yet the jute-based board fulfilled the requirements of commercial particleboards and it is also free from toxic formaldehyde!
Juteborg Sweden AB is open for partners who would like to join the JutePart™️ product-development journey, which will give a great future business opportunity.
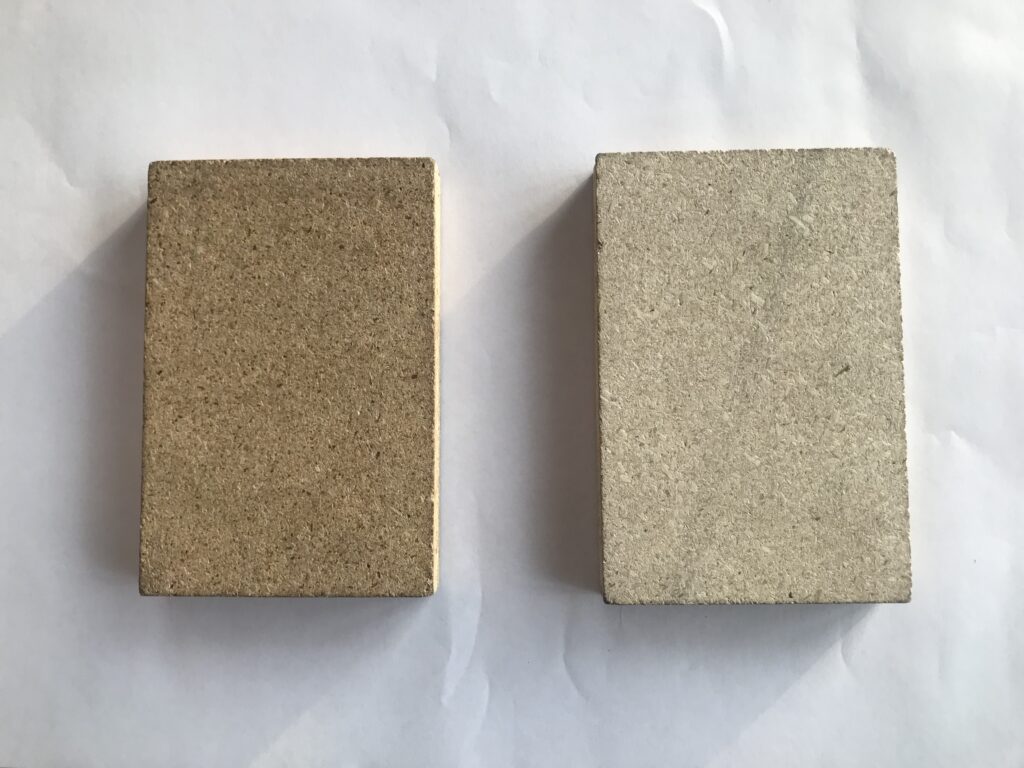
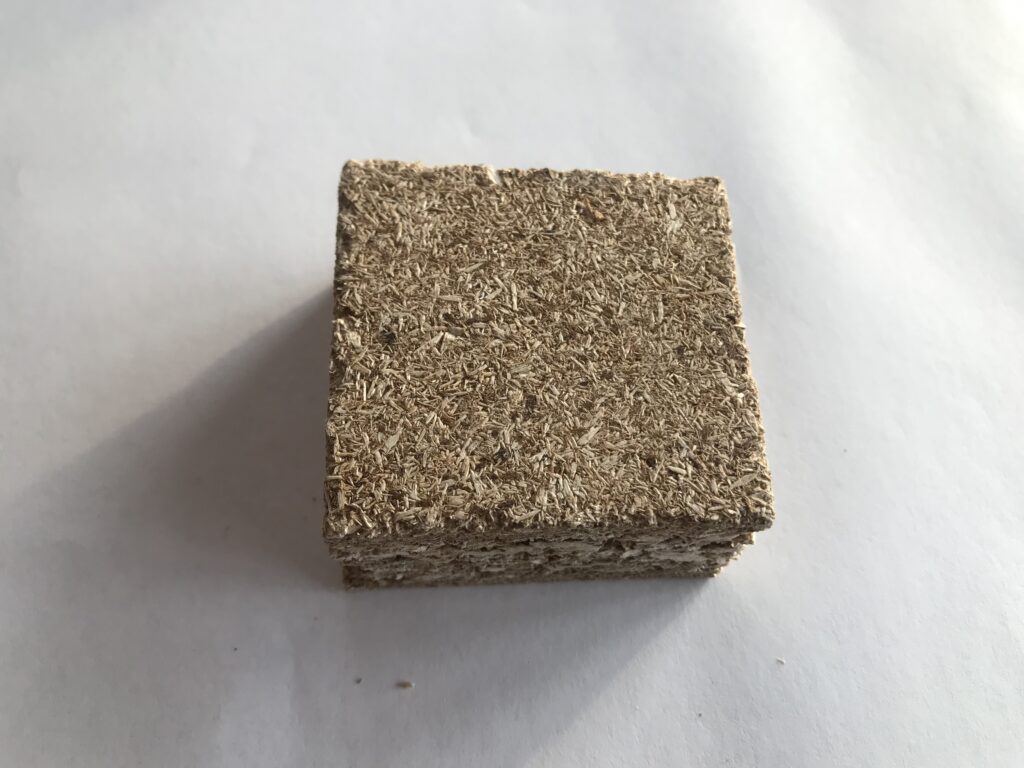
Juteborg Sweden AB aims to go to market with the most sustainable and lightweight particleboard in the world. Juteborg is a member of the Lightweight member programme, hosted by RISE, and the programme granted a research co-financing of “JutePart™️“ – The most sustainable particleboard.
The problem JutePart™️ with Ecohesives®️ is solving:
The market lacks boards in the construction/interior industry that are sustainable from all aspects and where the greatest possible circularity can be achieved. The construction industry is the fast lane to achieve the 17 UN global Sustainable Development Goals (SDGs) because of its huge volumes.
Since Jute is such a lightweight material due to the low density, Juteborg Sweden AB predicted that JutePart™️ particleboard should weigh approximately 25-30 % less than ordinary particleboard made out of wood.
Lighter particleboards mean energy benefits during transport and lighter buildings altogether, meaning other facts like, e.g., different considerations for the foundation It will also lead to significantly better working environment on the construction site.
Ordinary wooden particleboards on the market also contain formaldehyde, which is a toxic chemical. The environment is at risk from being polluted during the whole lifetime of the board, both during production and use, as well as at the end-of-life when the board is discarded. Current formaldehyde-containing adhesives in the particleboard must be replaced.
Jute is the most sustainable material in the world. Full sustainability is achieved by meeting the three pillars of sustainability: economic sustainability, ecologic sustainability, and social sustainability.
Social sustainability
Juteborg’s focus country is Bangladesh, the world’s second-largest producer of the world’s second-largest natural fibre in volume (only after cotton) – jute. Bangladesh has a population of 170 million people. Almost 1/3 of them is depending on the jute industry in one way or the other. When uplifting jute in the value chain, and refining jute in the country itself, 50 million people can be uplifted, and half of them are bottom of the pyramid people, earning 1,6 USD/day.
Ecologic sustainability
In Bangladesh, there is three crops/year. Two crops of rice and one crop of jute on the same land area. Jute is grown during the monsoon season (3-4 m high in 120 days) when it is the only viable crop to grow. Other crops would be flushed away in the monsoon heavy rains. Thanks to the robust root system of jute it is resilient and also prevents for further land erosion.
So, growing jute does not take away the land area from food production, which is a vital argument.
Growing jute in crop rotation with rice or other vegetables also ensures that there is no need for fertilizers and pesticides for the next rice crop. This is also an economic benefit for the farmer who saves 30% on his/her income, not having to buy the chemicals, and it ensures a healthy and ecological soil quality.
Jute cultivation absorbs much more carbon dioxide and releases much more oxygen than trees. One hectare of jute absorbs 15 tonnes of CO2 and releases 11 tonnes of O2 in one season (4 months).
Economic sustainability
The natural fibre of jute is cost-effective and performs very well in price comparisons. For Bangladesh, jute was the largest export income until the 1970s. It was reduced to no 3 on the list after the garment- and the plastic industry.
Juteborg Sweden AB has, together with influential people, seen to that the climb has begun. Going from low-valued products, such as sacks and ropes, to high-tech innovative Jute-based materials, the interest of growing jute is increasing. Now it is no 2 on the export-income list. Also, when uplifting 50 million people, most of the utter poverty, these people will also gain greater economic freedom.
When you harvest jute, you put them in bundles under waiter for 2-3 weeks so that they will undergo a retting process in order to extract the fibres from the stick. The fibres are sold on the market and the stems/sticks become a residual product with very little value and is mainly used by the farmers as fuel for cooking. Juteborg is now working on projects that aim to ensure that the sticks will also mean an additional income for the farmer.
2019, UN pointed out jute and allied fibres and signed a resolution in which the UN wants to promote the jute industry in developing countries to invest in Jute cultivation.
It has been clear that the utilization of jute can speed up the achievement of the 17 SDGs.
Juteborg targets all 17 SDGs in our work conducted in the company and we succeed there thanks to our cross-industry focus, our circular model and our:
Farmer to Factory Jute Supply Chain™️ (F2F™️)
Juteborg initiated the project F2F™️ in 2016 through a feasibility study led by Inclusive Business Sweden and financed by the Asian Development Bank.
Juteborg created the project because the company strives to take market shares in sustainable production and there certified and traceable products are required.
The intention is to certify, trace, and ensure the process from the very seed to the finished product in the factory, but also to ensure that the farmer gets a fair price. In calculations, the farmer will receive 4 times higher income during the Jute season than what he earns today. Juteborg is now making the last steps on an ongoing project since 2018, where we will, as one deliverable, validate F2F™️.
The project “JutePP®️ – the sustainable alternative for plastic products” is co-financed by the Nordic Development Fund via the Nordic Climate Facility in their program “Testing green business”. For the first time in history, Jute farmers met with Jute mill owners, intermediaries, and even the Jute Minister to discuss challenges and opportunities in jute production.
Juteborg’s goal is to start JutePart™️ production in Bangladesh with partners.
The global particleboard market is worth 19 billion USD and increases 6%/year. Right now, and much due to the climate crisis, sustainable solutions are required in the construction industry, an industry that has had fairly new sustainability wake up.
JutePart™️ particleboard has great potential due to its light-weight properties and the bio-based adhesive, Ecohesives®️, to take large market shares internationally, in the replacement of today’s particleboards of wood and fossil-based formaldehyde glue. For Juteborg this means a new segment and another step into the construction industry.
First out was JutePP®️ – Jute-fibre reinforced plastic granules for injection moulding and 3D printing. Volume production of the granules is starting in Bangladesh Q1 2021.
Research
Adhesives for particleboard production are today mainly prepared from polymers derived from fossil-based resources. With the increasing concern for the environment, it is necessary to find alternatives derived from biobased resources that can replace fossil-based polymers.
Furthermore, most of the fossil-based adhesives used today contain hazardous chemicals, e.g., formaldehyde, that have a negative impact on the environment and human health.
To enable the replacement of fossil-based adhesives with biobased and non-toxic alternatives, it is important that the adhesive properties in terms of bond strength, water resistance and heat resistance are similar, and that the alternative can compete in terms of cost.
Hemicelluloses are a by-product from the pulp industry. From environmental and economic perspectives, it is preferable to utilize all components from wood and decrease the amount of low-value by-products. Pulp-derived hemicelluloses have previously been evaluated as binders together with wood particles in the preparation of particleboards.
Hemicelluloses alone cannot be used as particleboard adhesives due to their limited bonding performance, especially regarding the water resistance. Therefore, a biobased co-component has been used as a dispersing agent, improving the water-resistance of the particleboards.
Encouraged by the very promising results from the KTH team’s earlier studies on wood particleboards, in this study we explore the possibilities of using jute particles together with the biobased adhesive Ecohesives®️, with the prospect of preparing strong particleboards of low density.
Results
The density of the prepared jute particleboards was measured to 0.4 g/cm³. This can be compared with the density of the wood particleboards prepared in our lab, which is typically around 0.7 g/cm³, i.e., the jute particleboards are very light.
The internal bond strength (IB) was determined for jute particleboards with different moisture and adhesive content. Results for wood particleboards prepared in the KTH lab have been added for comparison, Figure 4. According to the standard SS EN 312, boards for furniture in indoor use, with thickness 6-13 mm, should have an IB of minimum 0.4 MPa.
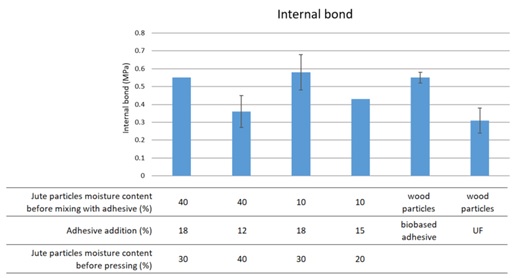
The density of these particleboards was very low, almost 50% of regular wood particleboard. At the same time, the performance of the particleboards was very good; by choosing the right parameters, the particleboards fulfil the performance requirements regarding internal bond strength of commercial particleboard used in indoor applications.
This research project has shown great potential to create the world’s most sustainable and light-weight particle board, JutePart™️ with Ecohesives®️, where Juteborg will replace wood with jute stick (residual material) and fossil-based and toxic formaldehyde glue with a bio-based, non-hazardous glue from sidestreams from the forest industry.
Contact person in JutePart™️ project:
Christina Östergren, CEO and Co-founder of Juteborg Sweden AB
Email: christina.ostergren@juteborg.se
Juteborg Sweden AB team
Christina Östergren, Else-Marie Malmek, Abir Hossain
Skärvallsgatan 6B, SE- 426 79 Västra Frölunda, Sweden
www.juteborg.se
www.farmer2factory.com
KTH Royal Institute of Technology team
Linda Fogelström, Eva Malmström, Tijana Todorovic
KTH Royal Institute of Technology, School of Engineering Sciences in Chemistry, Biotechnology and Health, Department of Fibre and Polymer Technology, Teknikringen 56-58, SE-100 44 Stockholm, Sweden
https://www.kth.se/fpt/coating-technology/research/malmstrom-group-1.911859